Generally speaking , when talking about moving cable , robot cable , towline cable , we mean similar high flex cable that could be used for drag chain system , so they can also be called drag chain able , dynamic cable .
Drag chain cable had been widely used for industrial applications , and customers sometimes ask , is drag chain cable the same as robot cable , moving cable and towline cable ? This article will answer this question, and introduce the details for these cables.
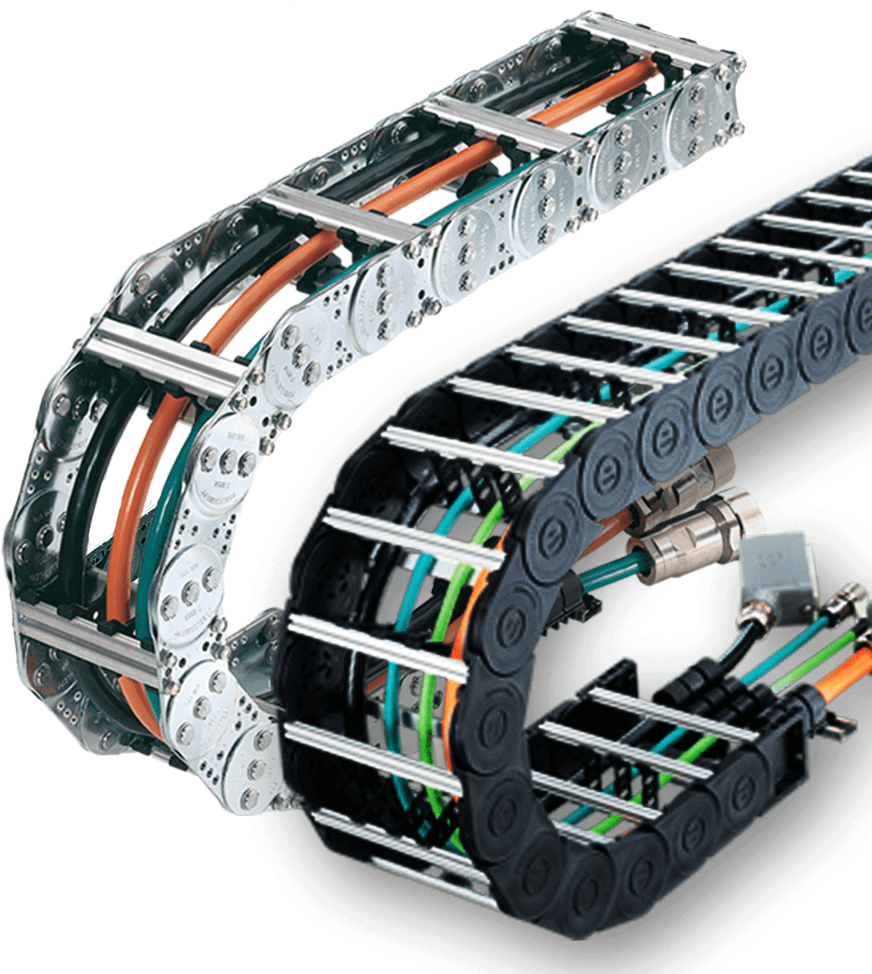
Is There Difference Between Moving cable , Robot cable , Towline cable , Drag Chain Cable
First let's introduce about these cables :
Robotic Cables
They are designed for robotic applications where the cables need to be flexible and withstand repetitive motion. They are usually made of materials that are resistant to abrasion, bending and twisting. Robot cables also typically have a high degree of electromagnetic shielding to reduce interference.
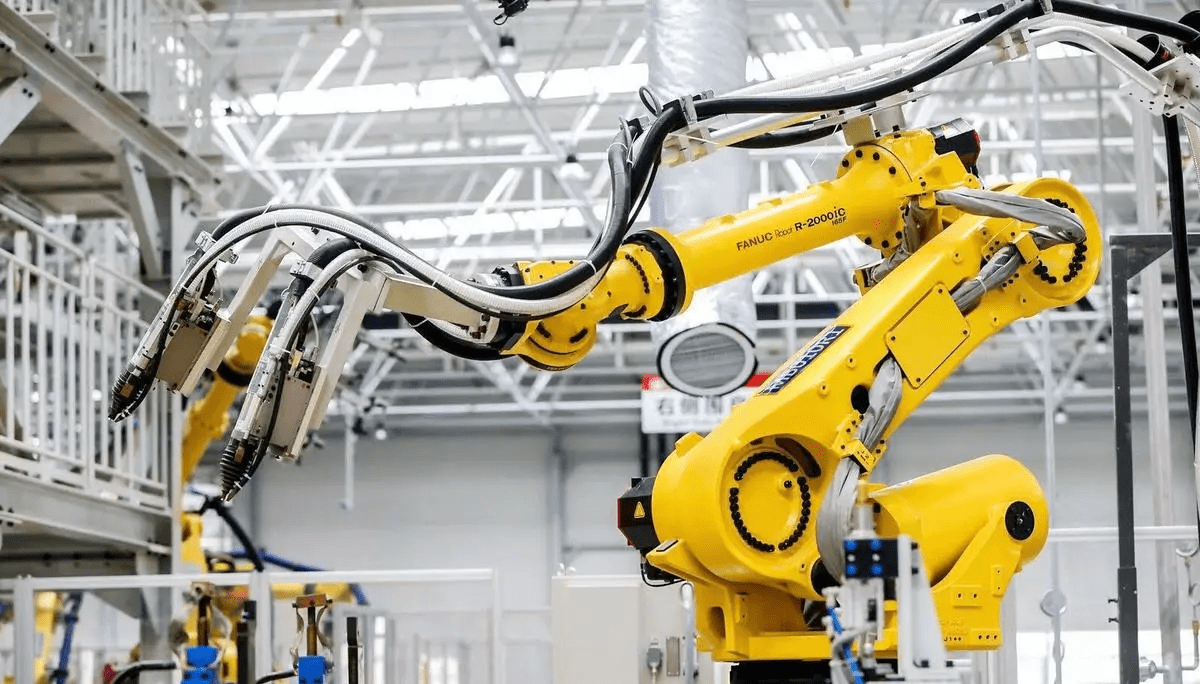
Moving Cables
They are similar to robotic cables in that they are designed for applications where the cables will be subjected to repetitive motion. However, moving cables are often used in applications where the motion is not as extreme as that of a robot. Moving cables are commonly used in industrial automation, conveyor systems and machine tools.
Drag Chain Cables
They are also called towline cables , and are designed for use in cable trays or drag chains to guide and protect cables and hoses in dynamic applications. These cables need to withstand constant bending and flexing, as well as exposure to abrasion, heat and oil. Drag chain cables are commonly used in robotics, automation and machine tools.
Common Features
From above content, we can find out the drag chain cable , robot cable , moving cable have same features have following :
High Flex
Whether it is robot cable or moving cable and drag chain cable, they are always bent, twisted and flexed in the application. If it is an ordinary cable, the cable insulation layer is very prone to wear and tear, the conductors may be broken , which will lead to cable failure.
Highly flexible cables are designed to withstand the bending and flexing that occurs as the cables move with robots and drag chain systems. These cables are made from a more flexible material than standard cables, allowing them to bend and twist without cracking or breaking. Additionally, high-flex cables have more tightly-bundled small conductors, which helps prevent cable fatigue.
Wear Resistance
In automated systems, towline systems, and robotic systems, cables are subject to repeated friction and pull from winches, pulley systems, or towline systems, and conventional cables are severely worn and torn. The cable may also rub against other surfaces or itself, causing abrasion and potential damage. Over time, this can cause the cable to weaken or even break, which can be dangerous and lead to accidents or equipment failure.
Abrasion resistance is therefore very important for moving cables to ensure they can withstand the repeated stress and strain of their intended use without damage. Cables with high abrasion resistance are less likely to fray or break, extending their life and reducing the likelihood of costly repairs or replacements. In addition, wear-resistant cables help maintain the safe operation of machines and equipment, protecting workers and the equipment itself.
Bending And Twisting Resistance
Moving cables, robot cables and drag chain cables are designed for applications that need to withstand constant movement, bending and twisting. Therefore, they need to have excellent resistance to bending and twisting to withstand these types of stresses and maintain their performance and reliability over time.
Flex resistance is important because mobile cables need to be able to withstand the repeated flexing and flexing they will experience during use without breaking or creating cracks in the insulation. Cables that lack proper bending resistance can develop kinks or other deformations that can cause signal loss, short circuits, or even complete failure.
Torsion resistance is also important, as moving cables may experience torsion as they traverse their intended path. These forces can cause the cable to twist or coil, which can cause signal interference, increased friction, and can damage the cable over time.
Difference Between Moving Cable , Drag Chain Cable , Robot Cable
As we know these types cables are all dynamic cables , should be high flex , have good wear resistance , bending resistance , twisting resistance , don't have big difference . For some customers may need cable for robots have much stronger twisting resistance , and corrosion resistance , so the cable producer may strengthen these performance , and for drag chain , towline system , may need the cable have good shielding performance , the cable manufacturer may also strengthen the shielding performance, but these are the key features.
Composition Of Moving Cable, Drag Chain Cable , Robot Cable
The comosition of these cables are the same as following:
1. Tensile center
The center of the cable needs to be filled with a center wire according to the number of cores and the space where each core wire intersects. This method can effectively protect the twisted wire structure and prevent the twisted wires from drifting to the center of the cable.
2. Conductor
The cable should choose the most flexible conductor. Generally speaking, the thinner the conductor, the better the flexibility of the cable, but if the conductor is too thin, the cable will be entangled. After rigorous experiments, the best diameter of the appropriate single wire is selected, which has the best tensile capacity.
3. Core wire insulation
The insulation in the cable must not stick to each other, and the insulation needs to support the conductors inside well. The core wire insulation is generally made of high-pressure formed PVC material.
4. Stranded wire
The stranded wire structure should be twisted in bundles.
5. Inner sheath
Located outside the conductor and inside the shielding layer, non-woven fabrics can be used to ensure that the twisted wire structure will not be scattered.
6. Optimized braid angle for shielding
Tightly braid the shielding layer outside the inner sheath. Loose braiding will reduce the EMC protection ability and the shielding layer will quickly fail due to shielding breakage. The tightly woven shield is also resistant to torsion.
7. Cable jacket
The cable jacket is made of different modified materials have different functions, some are UV-resistant, some are low-temperature resistant, some are oil-resistant and cost-optimized. But all of these cable jackets have one thing in common, high abrasion resistance, and don't stick to anything. The cable jacket must be highly flexible but also have a supporting function. Of course, it should be high-pressure formed, and PVC and PUR are more commonly used.
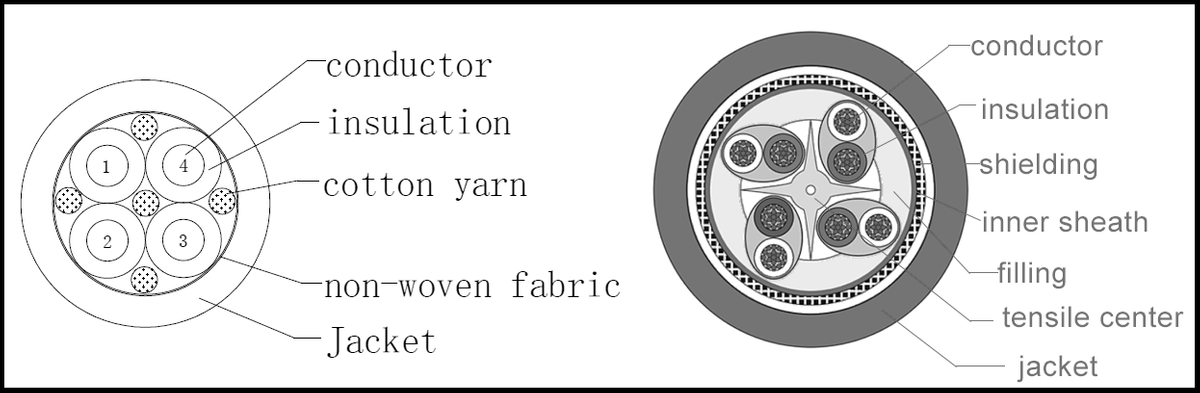
How To Choose Moving Cable , Robot Cable
Choosing the right moving cable will depend on a few factors, such as the type of application, environment, and required specifications. Here are some steps you can follow to choose the right moving cable:
Cable type
Depending on the application, you may need to choose from various types of cables, such as power cables, signal cables, data cables, or hybrid cables.
Working environment
The environment where the cable will be used is also an important factor. If the cable will be exposed to harsh conditions, such as extreme temperatures, chemicals, or abrasion, then you will need to choose a cable that can withstand those conditions .
Movement features
You need to consider the minimum bending radius of the cable, the moving speed of the cable, and the bending life of the cable, such as 5 million times, 20 million times.
Physical Characters
Such as size of the cable , length , tensile strength.
Electrical specifications
Finally, consider any other specifications that the cable will need to meet, such as voltage, current, frequency, or shielding requirements.
What Moving Cable , Drag Chain Cable , Robot Cable Do CAZN Have :
1. Industrial ethernet cables such M12 X coded cable , M12 D coded cable , M12 A coded to RJ45 , all can be made with moving cable.
2. A coded M12 cables which could be used for sensor , actuator , power and data connection for automation.
3. M8 cables to connect sensor and actuator in automation field can also be made with drag chain cable.
So, above is most of the informations for drag chain cable , moving cable , robot cable , if you have some questions , or want to add or correct some content , welcome to contact us.